In traditional retail models, business owners normally buy the products from various suppliers and resell them in their stores, websites or marketplaces. However, the retail industry has recently witnessed the rise of M2C – Manufacturer to Consumer model, which is also known as D2C or Direct to Consumer model.
What is a M2C business?
In an M2C business, the manufacturer directly sells what they produce to the customer without any third-party distributor. In doing so, products can be distributed to the market at a faster rate. Also, the customer can enjoy lower prices because they can buy directly from the manufacturer.
M2C is also a great option for small and medium businesses to compete against the “big players” like Walmart. The business owner can also keep a larger slice of the profit to their business. Some people even consider M2C to be the new era of e-commerce, especially for niche markets.
However, as M2C is still a rising star, it has not attracted the adequate attention of many software providers.
Most of the solutions for M2C business nowadays are traditional manufacturing software, suitable for a manufacturer rather than a retailer. Thus, these systems normally give them a hard time integrating ERP to sales channels such as point of sale, Magento E-commerce websites, and marketplaces.
If you’re a business owner doing manufacturing and selling your product on Magento, keep on reading. This article will help you find the right manufacturing software to optimize both your manufacturing and selling operations.
What should business owners prepare when selecting a manufacturing software?
Before we go into the details, here are a few things that you should prepare to find the best manufacturing software for your business.
Understanding your business needs and goals
It’s very important for business owners to think about their business needs and goals before doing any research about manufacturing software.
For instance, your greatest need could be to sell on both your Magento site, marketplaces like Amazon, and offline channels with real-time data synchronization. Similarly, do you expect to open a few more outlets in the future and want the manufacturing software to scale up with your business?
Under-scaling is a common mistake when retailers look for a business solution. A manufacturing software system that is good for now may not be as good in a few years. So thinking ahead may save you many troubles in the future.
You can also begin with the problems of your current manufacturing process/software and want the new system to tackle.
Based on the business needs, goals, and problems, you can produce a list of realistic expectations about the manufacturing software, and the changes you would like to see in your organization when the new system is implemented.
Listing out the features, priority & budget for your manufacturing software
Businesses of different sizes and natures require very different approaches. A simple business would normally require a simpler process than a big conglomerate. So you’d want to identify which features you want to have in the new ERP system. A clear vision of the features, priority, and budget can keep you focused on what really matters for your business and streamline the selection process.
What are the components of manufacturing software?
In this article, we’ve listed some components of a manufacturing software system. We’ve arranged the features according to their level of importance, starting from the most fundamental ones for small businesses.
Must-have features
Manage Inventory:
The manufacturing software system must help you keep track of your inventory, including the stock level of the materials and finished product.
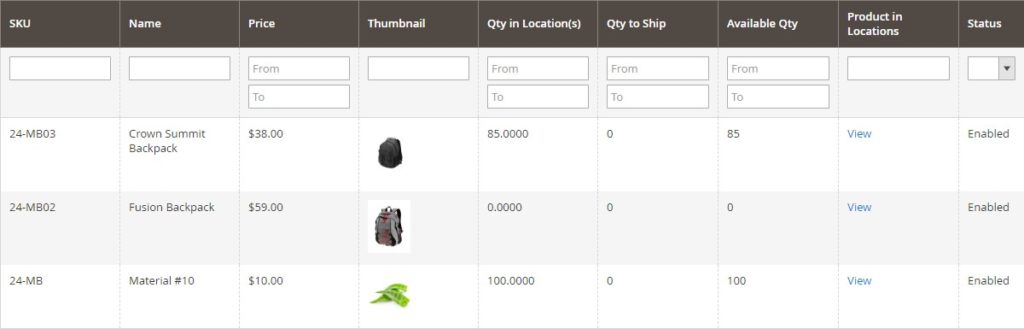
Also, this system should be able to tell you when your stock level is running low. With this, you can make purchases or start manufacturing to prevent sales disruption due to out-of-stock problems.
Manage Bill of Materials
A crucial part of the manufacturing process is tracking product formula. It means that by looking at the system, the staff can tell which ingredients and how much is needed to produce a unit of a finished product.
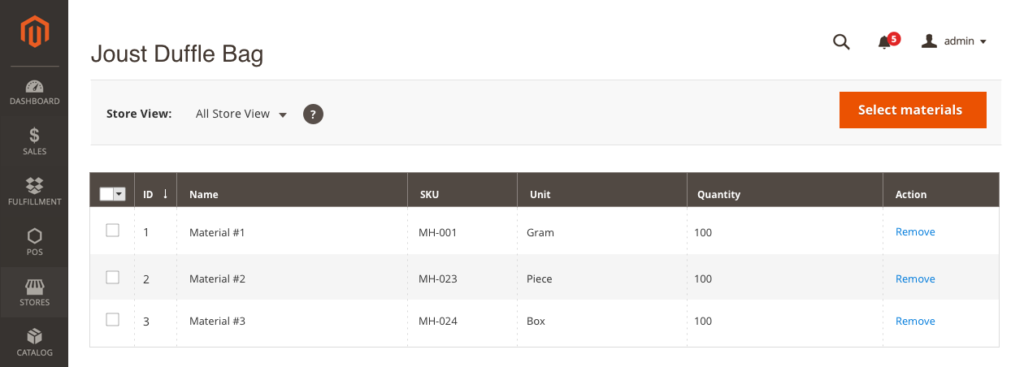
Some businesses also need to manage and display steps of the manufacturing process for each product. This feature is quite helpful if the process is complicated and the staff needs guidance.
Manage production plan/ Manufacture order:
This is the core of a manufacturing software system. Essentially, this feature involves planning the products and the quantity to produce. Also, the system should be able to generate the material list from the production plan. The list should include the name and quantity of materials needed to produce the given amount of finish good.
Nice-to-have features
Aside from the fundamental features mentioned above, some ERP manufacturing software offers additional nice-to-have features:
Work schedule & calendar management
With this feature, business owners can work out their manufacturing plans ahead of time and arrange different plans.
Specifically, they can set the start date, finish date, expected lead time, or set the due date for each plan. Having a calendar that visually maps out all plans will give the manager an overview of their business. As a result, they can utilize resources in the most effective manner.
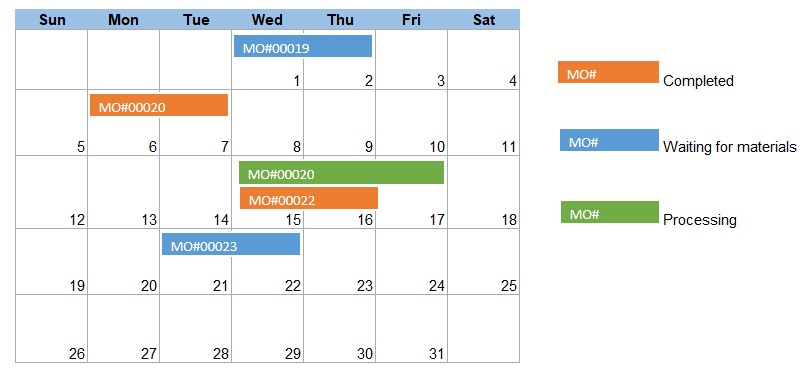
Lot number/serial number management
Many industries (such as pharmacy, food, or beverage) require high-level inventory management. They might require a lot and serial number tracking management systems.
Normally, business owners would need to manage two types of lot & serial numbers.
The first one is the lot and the serial number of the material. This helps the business owner know which provider they bought the material from. It also lets them know when they purchased the material. Thanks to this, business owners can utilize the material on a first-in-first-out basis and avoid the expired material problem.
The second type is the lot and the serial number of the finished product. This helps the business owner know which product and how much they produced. Business owners can also track inventory age to make the appropriate decisions, such as selling items of old age or running a promotion campaign.
Multi-stage production management
Some businesses have very complicated manufacturing processes. Thus, the manufacturing software needs to map out all the steps, duration, and instructions for each step. In doing so, the staff can follow the steps precisely during the manufacturing process.
Staff assignment
In some cases, the business owners want to limit the staff to a production batch or steps. Based on this, the manufacturing software will provide a different interface for the staff to interact. Ideally, the staff can only see their assigned steps.
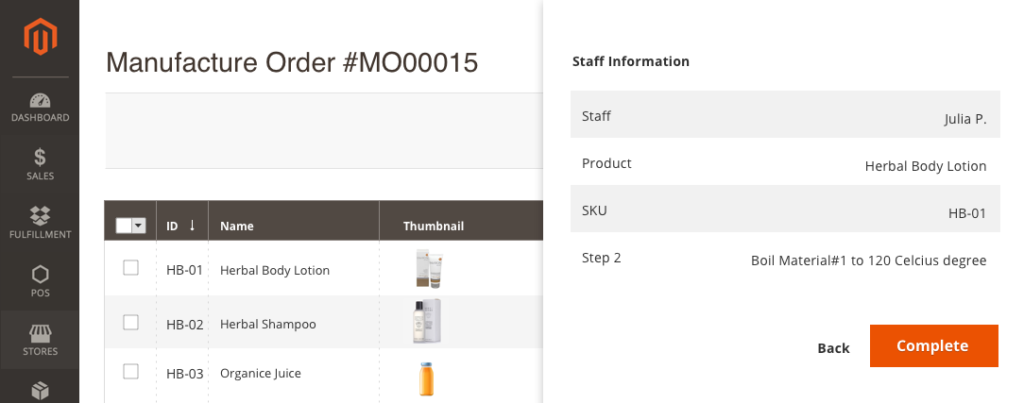
Plants/Machine/Human resource capability management
Every business has a limited production capacity based on their human resource and machines. Knowing this limit ahead of time can help business owners make better manufacturing plans and optimize their resources.
Reporting (history, variance,…)
It’s always a good idea to keep track of your manufacturing, including those performed in the past. An operation record gives you an overview of the production process and lets you see if everything went as planned.
You should also track if there are any variances in the production. For example, a product requires more material or the packaging process is taking more time. From here you can adjust your operation accordingly.
There are also many other cool features that the ERP systems available in the market have to offer. However, within the scope of this article, we only point out the ones that are directly related to the manufacturing operation.
Potential issues with manufacturing software
We recommend that you discuss all the possible potential issues with your manufacturing software provider. It’s always better to prepare and ask up front instead of finding issues when you’re already using the software.
Here are some common problems that our clients discuss with us when they use manufacturing software systems.
Limited or no integration with the online site/POS system
If you’re selling online, then this might be the biggest issue for you. Imagine that you’ve already manufactured your products, but your Magento website still displays the item as “out-of-stock”. The same issue can happen to your POS system.
Some manufacturing software providers claim to support integration with e-commerce platforms including Magento, but data synchronization can take up to a few hours. This is a huge issue as the customer can just walk to another store to purchase the product.
Problems with Kit/grouped/bundled product
Manufacturing software normally deals well with simple products (a product sold in just one piece). However, some of them tend to have a problem when products are sold in a group or as a bundle (think about a computer station with a screen, CPU, and mouse).
If you’re manufacturing and selling these types of products, make sure to discuss this issue with your solution provider.
Limited customization and update
There’s no one-size-fits-all solution for every M2C business. Normally, when the business owners need a feature that is not available in the default software, they have two options. They can suggest the feature(s) to the solution providers and wait for the product update. Another option is to request a customization of the default system.
With the first option, you may have to spend extra on an annual maintenance fee.
This option may take up to a couple of years. Also, there’s no guarantee that the new feature will be exactly the one you need.
The second option will guarantee that the feature is built the way you need. However, it will charge you extra cost for the time and effort the development team puts in.
These are some of the most common problems an M2C business might encounter in its operations. Make sure you’ve listed out the necessary features not covered by the software and discuss them with the provider. In doing so, you can have a full view of the cost-benefit analysis of the new system.
Conclusion
To sum up, it may take a lot of effort to select the right manufacturing software for your business. However, a good understanding of your business goals and need, along with a realistic list of expectations, can help you along the way and make the right decision.
Happy selling!
2 Comments
Do you mean you are developing an manufacturing module on Magento?
Thanks for sharing such nice information.